Table of Contents
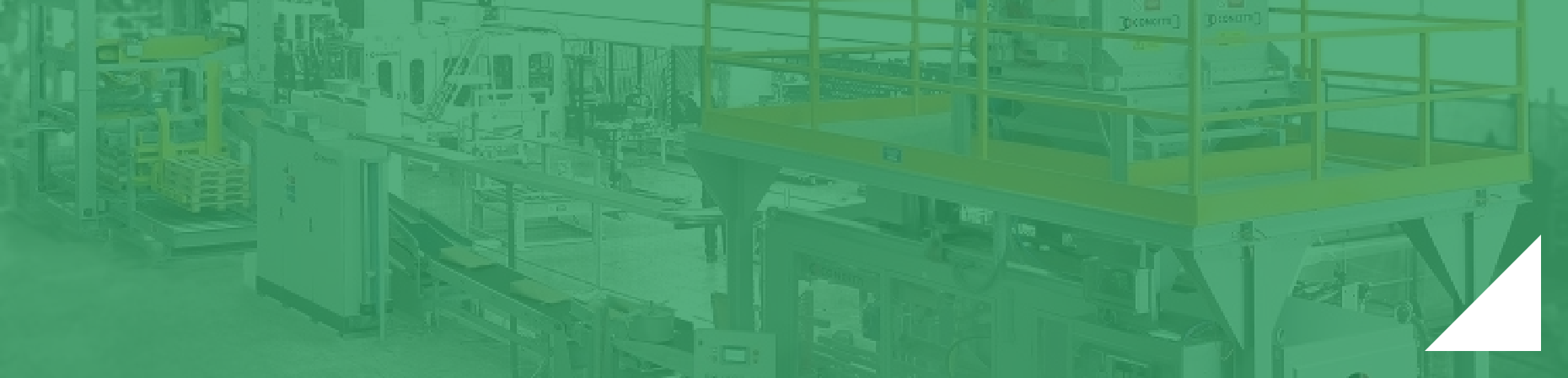
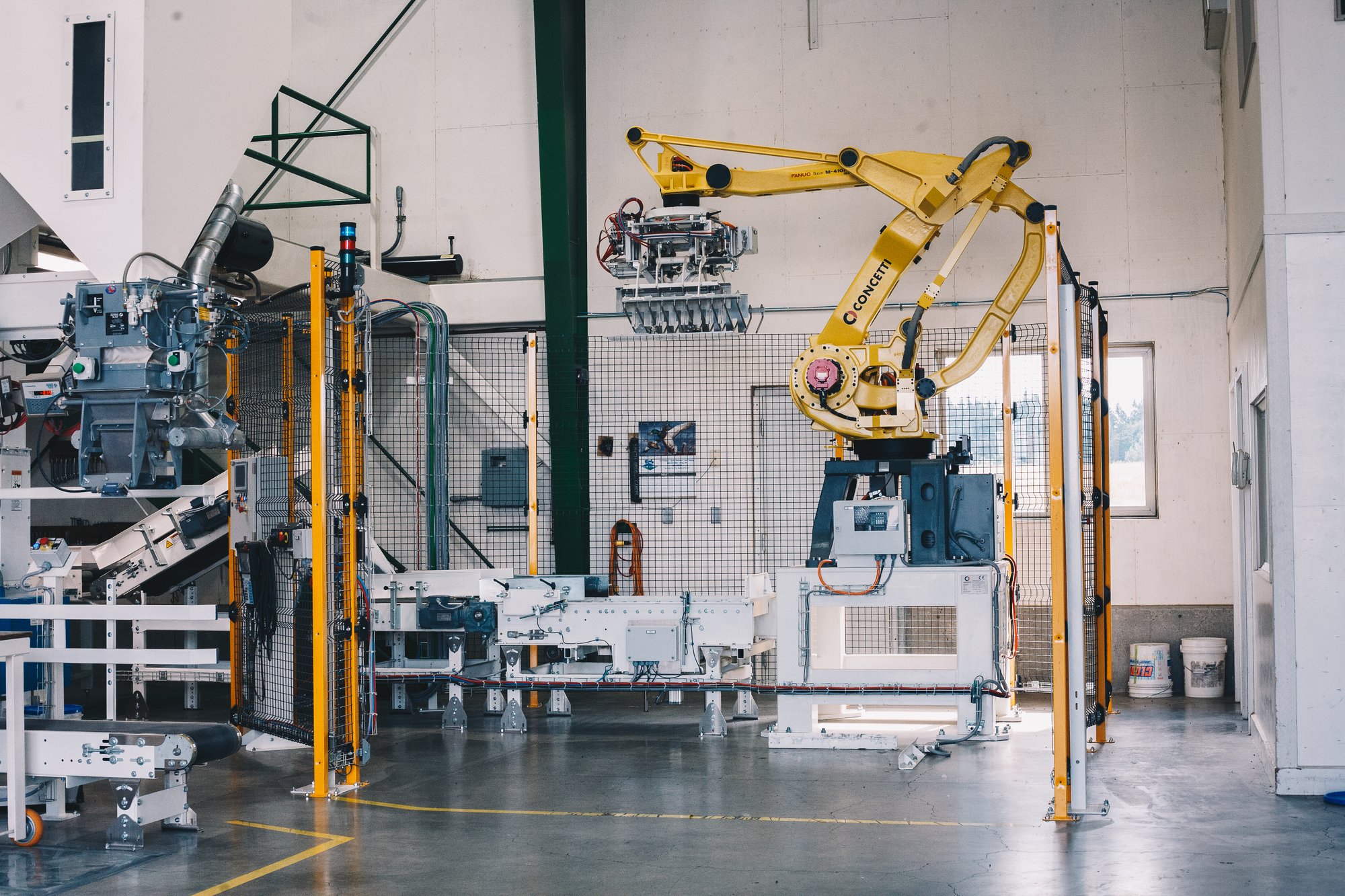
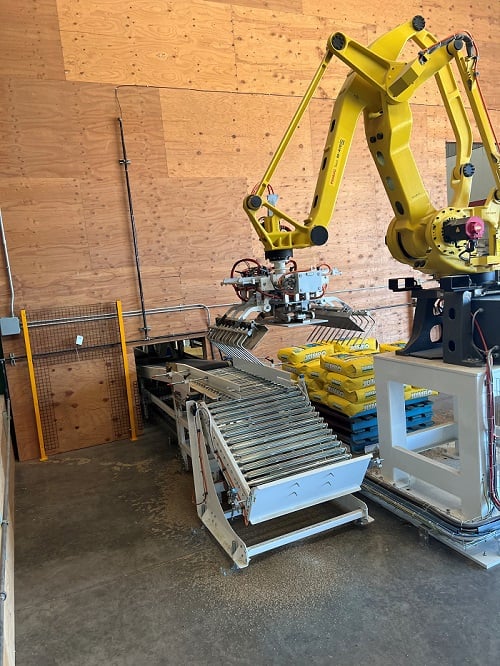
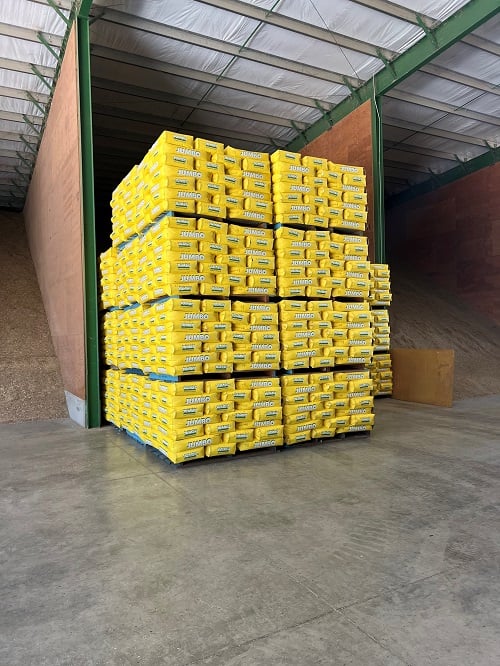
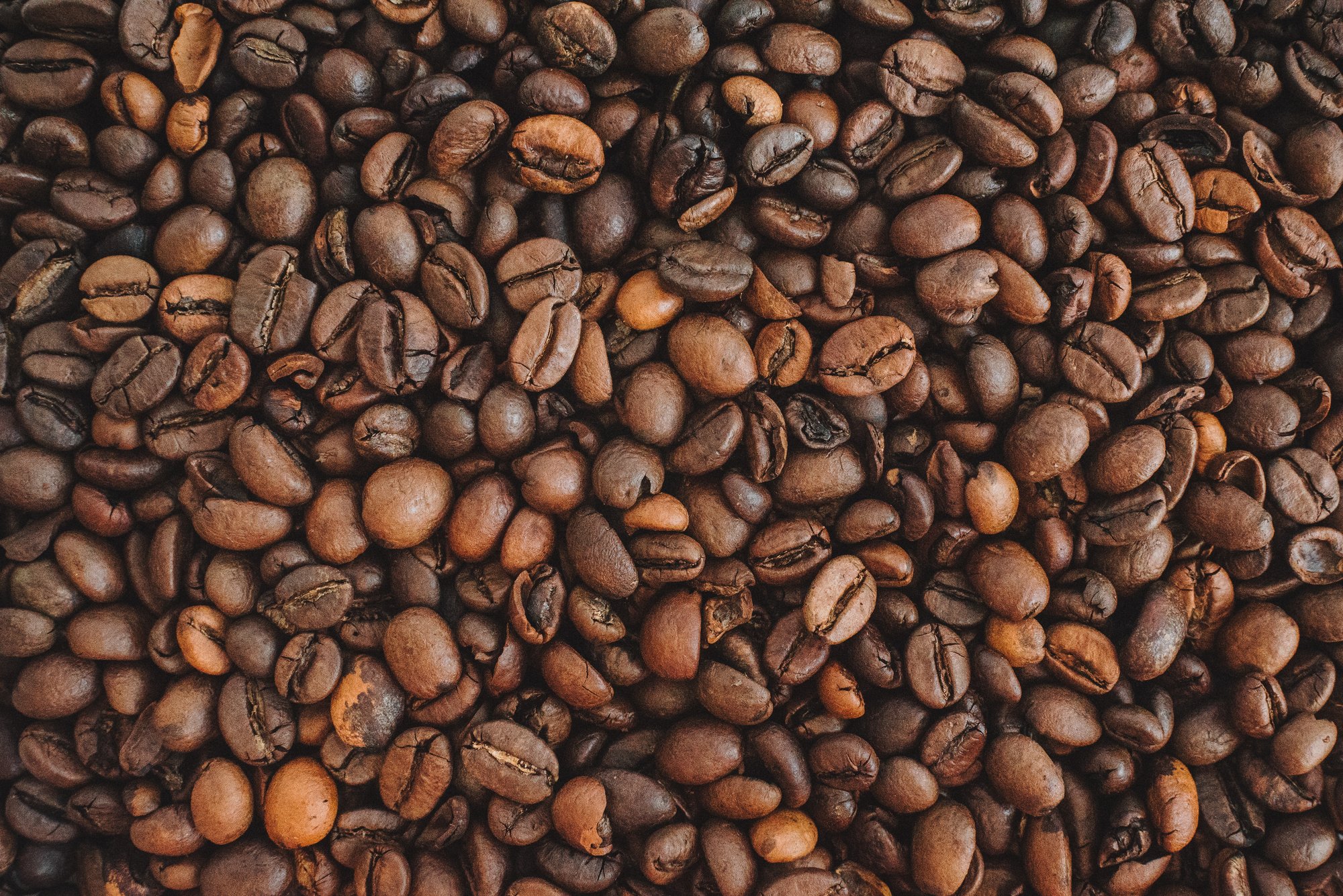
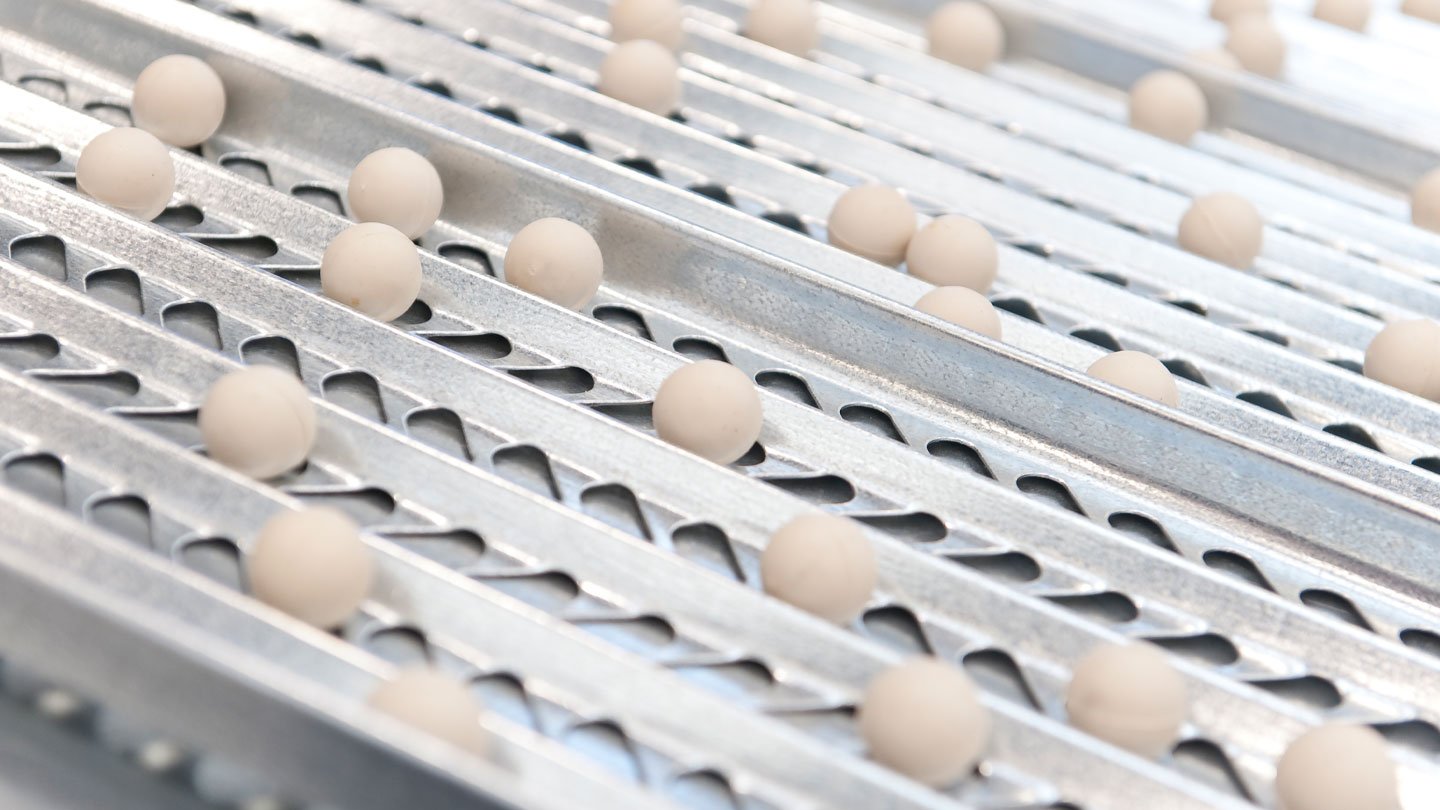
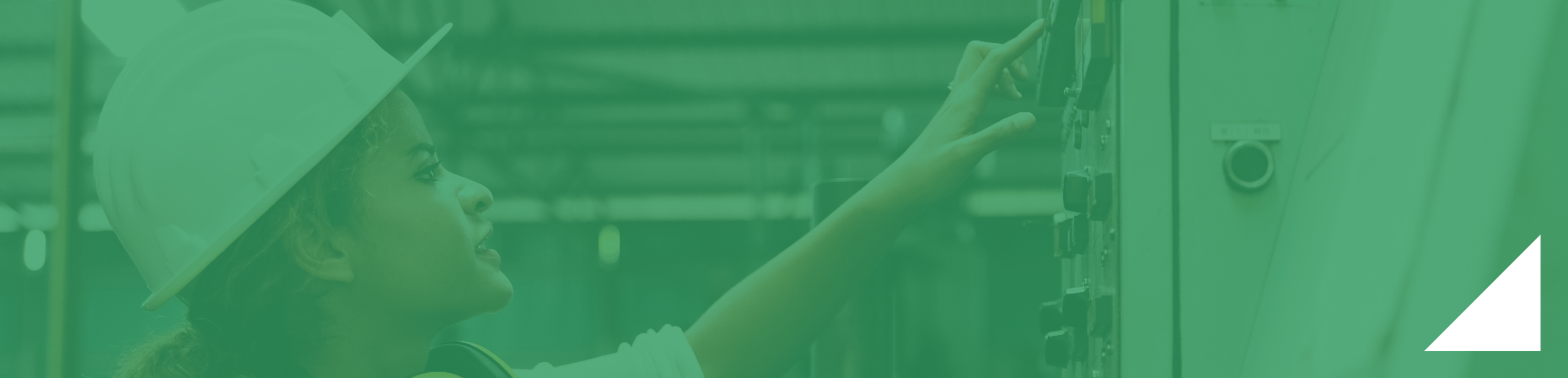
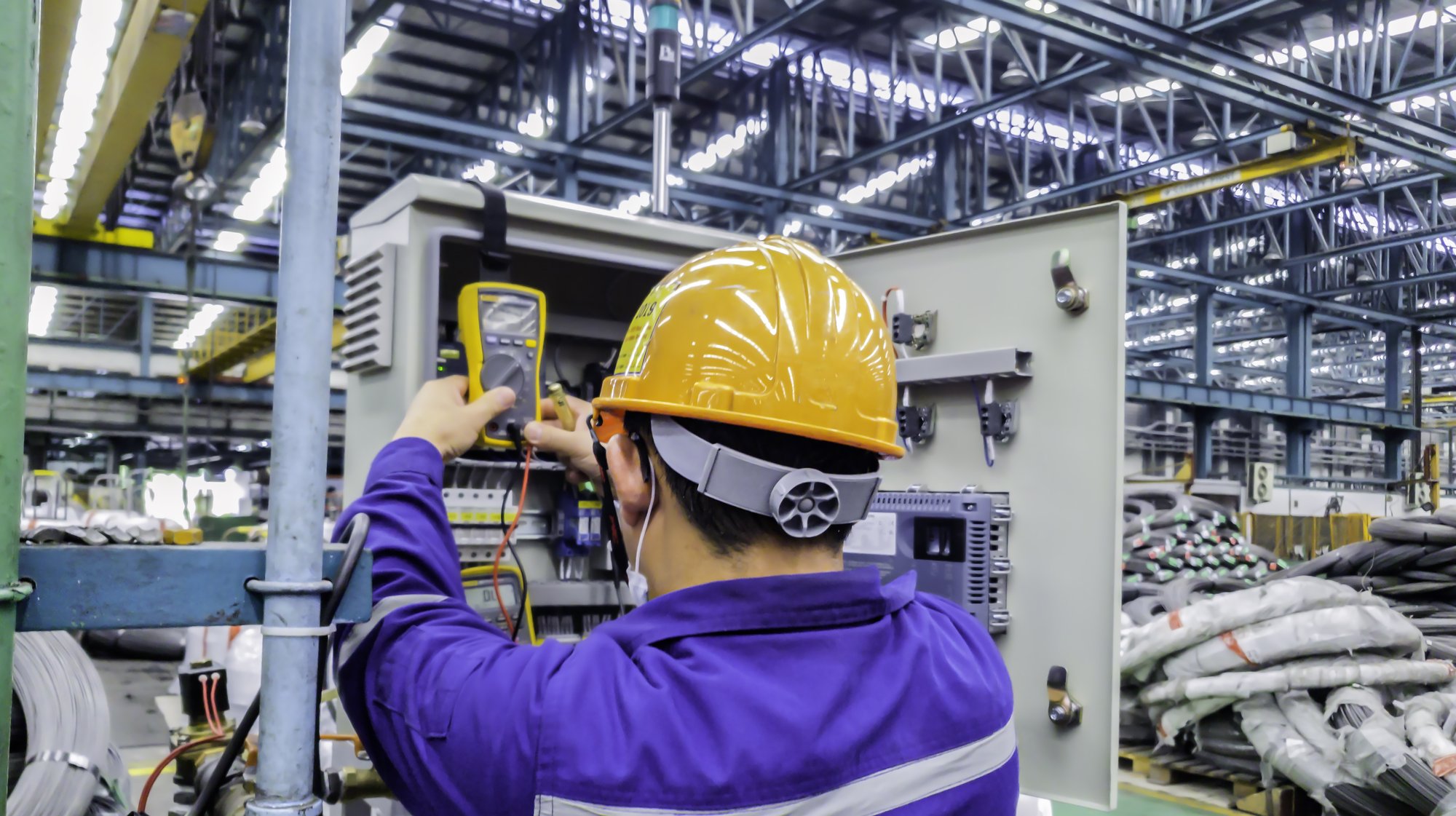
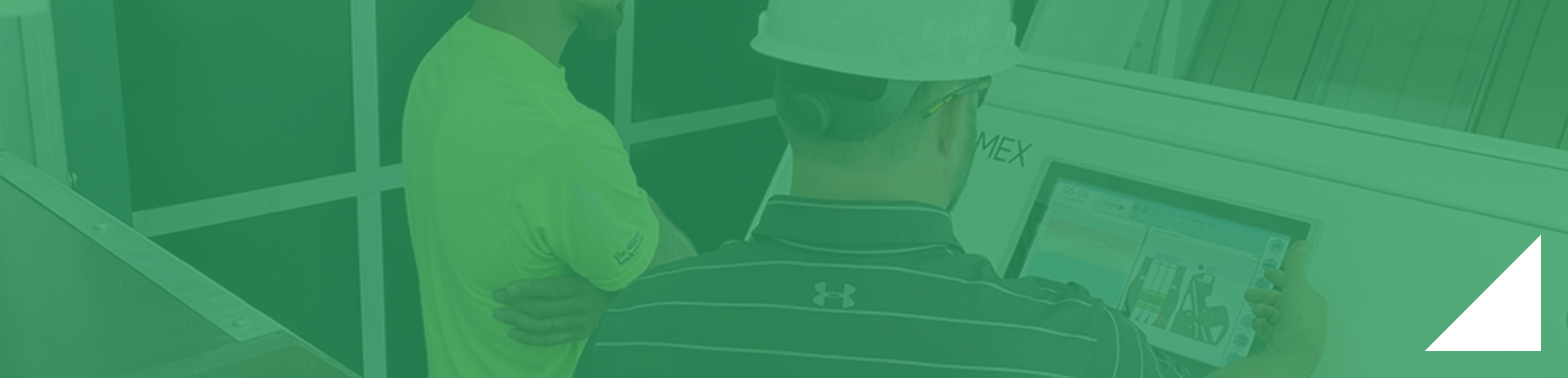
/Mckillip%20new%20building-700x524.jpg?width=700&height=524&name=Mckillip%20new%20building-700x524.jpg)
Transitioning bagging and palletizing processes to automated solutions enhances productivity, quality, and safety. For example, automated bagging and palletizing reduces injury risks from repetitive motion and heavy lifting for workers. The automated equipment is ergonomically designed to reduce the physical strain on your workforce. Employees also tend to be more satisfied and engaged when they are not required to perform mundane or tedious manual tasks.
These automated systems can bag and palletize considerably faster and with greater consistency than human workers speeding up production. As an added benefit, the reduced reliance on manual labor can lower personnel costs associated with these functions. Automated lines can be added easily when compared to hiring and training the additional staff necessary to increase capacity. Additionally, individual tracking and identification methods improve traceability so, if defects arise, sources can be isolated quickly and efficiently.
Automated equipment has much higher throughput compared to manual processes, which lowers associated labor costs. Automated systems can apply print, tags, and labels consistently and accurately, with far less human error. This results in less waste from misprints, incorrect tagging, and other associated defects.
Automated systems also have data collection capabilities that can be used to identify areas for quality and process improvements. And, for increased safety, workers are removed from those repetitive manual tasks that can cause injuries.
24/7 operation is completely feasible with automated equipment, and production output can be more readily adjusted by adding or removing the automated capacity as needed.
Air screen cleaners are high-capacity machines that sort products by size while removing dust and other lighter contaminants through aspiration. They work by running products across a series of screens to separate material based on size. This is a process that has been done for centuries, but modern cleaners do this much more efficiently and at high capacities. With routine inspection and maintenance, these cleaners are extremely reliable.
Many types of screen cleaners are unreliable and require a substantial amount of maintenance. Additionally, they rely simply on the screens to do all the work. Our cleaners offer aspiration both on the infeed and outflow of the machine to ensure that your product is free of lighter contaminants. Additionally, they are designed for easy access and maintenance, making them reliable for decades.
When employees don’t feel safe on the job, or they think that your company isn’t prioritizing safety enough, they’ll leave. Automation can take on the tasks your employees say feel unsafe or too risky for them to perform efficiently. Instead, employees can operate and oversee programmable machines that do those risky jobs on their behalf. This not only decreases physical injuries or accidents but also helps give employees a sense of security and wellbeing while on the job.
Lorem ipsum dolor sit amet, consectetur adipiscing elit, sed do eiusmod tempor incididunt ut labore et dolore magna aliqua.